Technologies are a vital part of R&D. Nestle engineers working in R&D in a variety of fields – from packaging and equipment, to food processing technologies and manufacturing new beverage systems such as Nespresso, Nescafé Dolce Gusto, Special. T and BabyNes.
Alongside engineers, of food scientists develop processes and technologies that enable the development of safe, nutritious foods and beverages while keeping us on the cusp of new developments in food science and technology.
Nestlé has developed, and/or is a world-leader in a large number of different technologies. Here are a few examples:
- Fermentation and probiotics: The Nestlé Research Centre was one of the first to look at the molecular interaction of probiotics with intestinal cells. We have sequenced several probiotic genomes, so that we can better understand their characteristics and mechanisms of action.
- Extrusion: We have strong expertise in hot extrusion (eg infant and breakfast cereals), co-extrusion (eg filled bars and snacks) and cold extrusion (eg ice-cream and chocolate).
- Healthier fats: We have also developed technologies that allow us to use natural vegetable oils instead of partially hydrogenated fats in our Maggi bouillon cubes and seasonings.
- Foam booster technology: This produces the creamy head for Nescafé Cappuccino, with less fat, and which is much denser and longer-lasting than regular foam. In 2002 we relaunched Nescafé Cappuccino with our new foaming mix products, which we created these using our foam booster technology.
- Malt extraction: We have developed a new process for malt extraction for Milo that meant less sucrose and more complex carbohydrates in the product. It was launched in Malaysia in 2006, and in 2007 it was rolled out across Asia.
- Portion dispensing systems: This know-how is essential for our beverage systems.
Nestle Capacity Planning
Capacity is the total maximum level of output a business can produce in a given period. This allows a business to meet the level of demand for a product.
Capacity utilisation is the actual output per annum.
Capacity planning is the process of determining the production capacity needed by an organization to meet changing demands for its products. In the context of capacity planning, design capacity is the maximum amount of work that an organization is capable of completing in a given period. Examples of this is the seasonality of products.

1. Evaluate current processes
A sound automation strategy begins by conducting a thorough assessment of existing business processes. It begins with a look at tasks and procedures that are highly labor-intensive, especially those that add little value. Tasks are that are the most time- and labor-intensive are those that are the top targets for automation.
2. Capitalize on existing automated systems
Many producers already have systems that are automated and integrated, operating on a common network or platform. However, full integration is the optimal state, where all systems across the enterprise are connected, with data shared across the organization.
Packaging, in particular, is an area where fully implemented integration has been elusive. Individual components and machines are integral parts of many such packaging systems. When one of those components is offline due to maintenance or repair, the entire packaging system can halt.
Integrating the whole system greatly lessens the reliance on one component and the unfortunate consequences that arise when that component breaks down.
3. Seek systems with intuitive controls
User-friendly automation systems are critical. Without them, there are likely to be higher training costs, especially as food and beverage manufacturing traditionally relies on an older workforce. Automation should use software that is easy to learn, use, and master to make adoption as frictionless as possible.
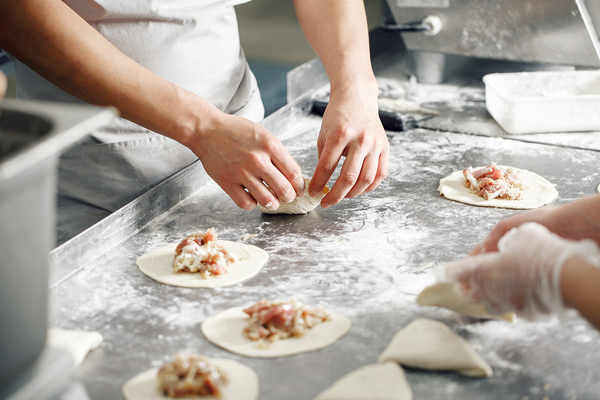
Many food producers still rely on manual processes. Automation can reduce production costs by identifying inefficient and low-profit procedures.
4. Use integrated platforms
Today, employees, leaders, and key stakeholders can be anywhere, using multiple device types to connect to systems. Increasingly, these devices are mobile. Your automation systems need to support multiple devices and be accessible and functional across platforms. Data needs to be easily accessible from mobile devices and not bind employees to their desks in order to access features.
5. Develop performance metrics
It’s important for manufacturers to establish measures, including key performance indicators that measure the impact and efficacy of the automation solutions that are implemented. Whether these measures reflect shortened lead times, less waste, shorter production cycles, fewer processing costs, or lower personnel costs, the need for measures against baselines should be determined, tracked and used.
These measures can inform not only performance but also, other opportunities for improvements and future purchases.
6. Focus on early payment choices
Many vendors provide valuable incentives for early payment discounts. These discounts can considerably reduce project costs, making the choice about adoption clearer for companies debating whether to fully invest.
NexTec Group helps companies identify the enterprise resource planning (ERP) tools necessary to integrate automation across the food and beverage company. With ERP, companies pull together data from operational, financial, sales, and customer relations areas, providing holistic looks at the information, reporting, and analysis necessary to improve operations.
We help companies find the right ERP solution to fit the needs, budgets, and automation tools in place and planned. Download the NexTec Ebook – Reduce food waste and improve to learn how NexTec can help select and implement an ERP solution that drives results.